TIG welding is a highly valued technique across various industries due to its precision and versatile applications.
A welder mastering this method must combine skill, experience, and knowledge of materials.
The technique allows for welding different metals such as aluminum, stainless steel, and titanium. In this article, we will explore the basic principles of TIG welding, the influencing parameters, and its various applications.
Principle and Functioning of TIG Welding
TIG welding, which stands for Tungsten Inert Gas, relies on creating an electric arc between a non-consumable tungsten electrode and the workpiece. When the welder pulls the trigger, an inert gas is released to protect the welding area, and current flows to the electrode. The tungsten electrode does not melt, but the arc generated heats the base material sufficiently to cause it to melt, allowing fusion between the parts. A filler metal, in the form of a rod, is added to complete the weld bead.
The TIG process stands out for its ability to provide high precision due to the stability of the arc and the ability to control current intensity, making it ideal for welding thin or delicate materials. This process is primarily used in industries where weld quality and resistance are essential.ers are properly adjusted and the right materials are selected.”
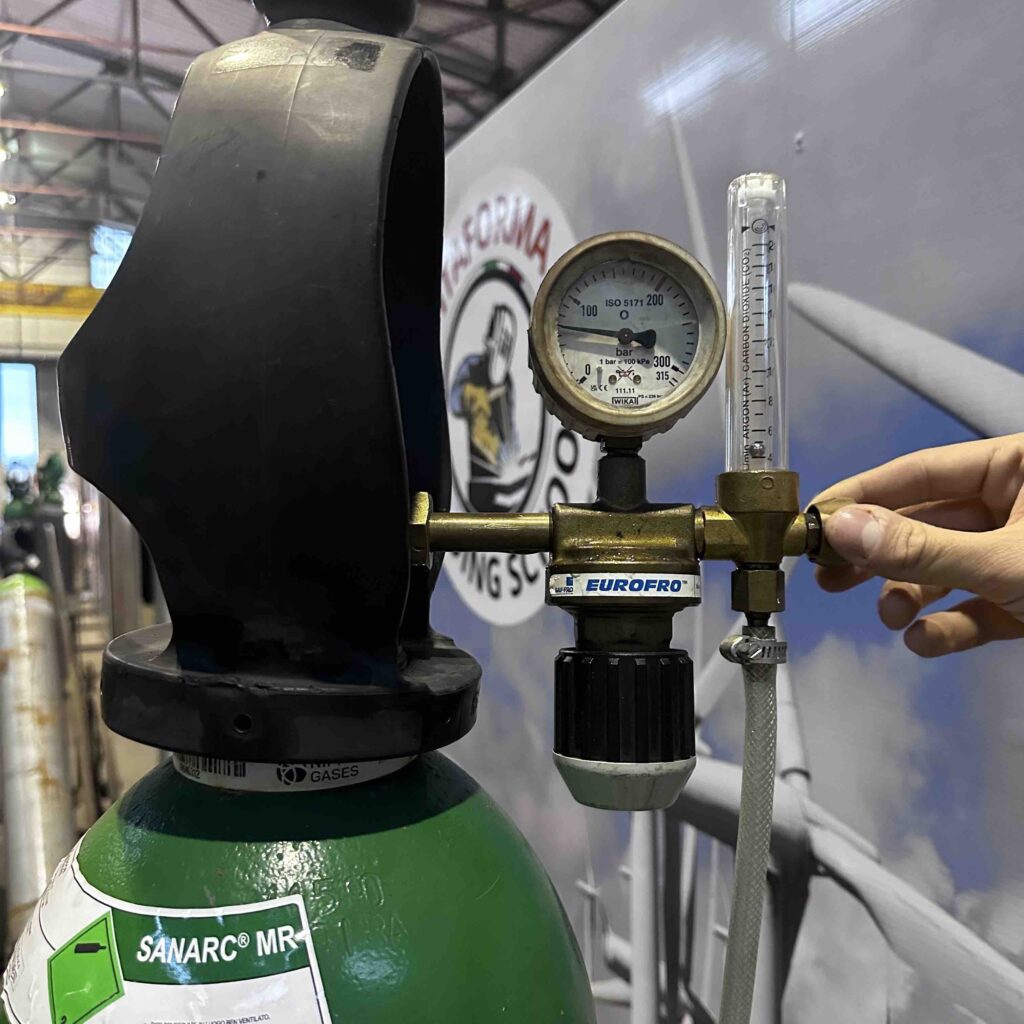
Welding Parameters and Their Influence on TIG Welding
The quality of TIG welding depends on several key parameters that must be adjusted according to the materials and thickness of the workpieces. These parameters directly influence the precision of the weld, the penetration of the metal, and the stability of the arc.
Welding speed and torch position:
The speed of the welder’s movement must be adjusted based on the thickness of the materials and the geometry of the weld. A too-fast speed may result in insufficient penetration, while a too-slow speed could cause overheating and warping of the material.
Choice of gas and flow rate:
Argon is the most commonly used shielding gas in TIG welding. Depending on the application, a mixture of argon and helium may be used to increase the energy of the arc, particularly for light metals like aluminum.
Electrode and preparation:
The tungsten electrode must be properly sharpened to ensure optimal arc stability. The sharpening angle varies depending on the material being welded. For aluminum, for example, a 90° tip is required to prevent irregular melting points.
The choice of electrode, its diameter, and sharpening are crucial for obtaining high-quality welds.
Applications and Advantages of TIG Welding
TIG welding has a wide range of applications in industries where precision and aesthetics are paramount. Here are some of the main fields of use:
Aerospace and Aviation Industry: The precision and cleanliness of TIG welding make it ideal for welding lightweight alloys and stainless steel used in aircraft and spacecraft structures.
Chemical and Food Industries: TIG welding is perfect for fabricating stainless steel components, which are commonly used in the chemical and food industries where durable and clean welds are required.
Automotive Bodywork and Repairs: TIG welding is used for repairing stainless steel bodywork or lightweight aluminum car parts.
Precision Work: TIG welding is widely used to weld thin sheets or in industries requiring aesthetically perfect welds, such as jewelry making or precision instrument manufacturing.
Advantages and Disadvantages: While TIG welding offers great precision and clean work with minimal smoke, it has the disadvantage of being slower, especially when welding thick materials. Additionally, it is crucial to master the machine settings to achieve optimal results.
The Importance of Practical Training to Become a Skilled TIG Welder and Obtain an Official Certification
To become a skilled TIG welder, practical training is essential. While understanding the theory behind welding principles, materials, and welding parameters is important, it is hands-on experience that allows one to acquire the necessary skills to master this complex technique.
TIG welding requires great precision and perfect control over the electric arc, welding parameters, as well as the use of shielding gases and electrodes. Only regular practice in real-world conditions helps develop the dexterity and skill needed to produce high-quality welds.
Moreover, undergoing specialized training, both theoretical and practical, and obtaining an official certification is crucial not only to ensure technical competence but also to guarantee safety on job sites.
A certified professional holds official recognition of quality and safety standards in the welding field, which is essential for working in demanding sectors such as aerospace, industrial part manufacturing, or metal structure construction. Comprehensive training also prepares the welder to adapt to technological advancements and master modern equipment, thus ensuring a successful and high-quality career in a field where excellence is paramount.
“In conclusion, TIG welding is a complex yet highly valuable process in applications where precision, quality, and weld strength are essential. Whether in the aerospace industry, stainless steel processing, or automotive repair, this process offers numerous advantages in terms of performance and aesthetics, provided that the parameters are properly adjusted and the right materials are selected.”