Overview of Arc Welding with Covered Electrode
Arc welding with a covered electrode, also known as process 111, is one of the most widely used welding techniques in industry. It involves creating an electric arc between the electrode and the workpiece, generating intense heat (around 3200°C), which melts the metal in the pieces and the electrode.
The electrode, in addition to acting as the filler material, is coated with a flux that protects the weld from oxidation and influences the nature of the molten pool.
This process is valued for its simplicity, flexibility, and low equipment cost, while ensuring strong and durable welds.
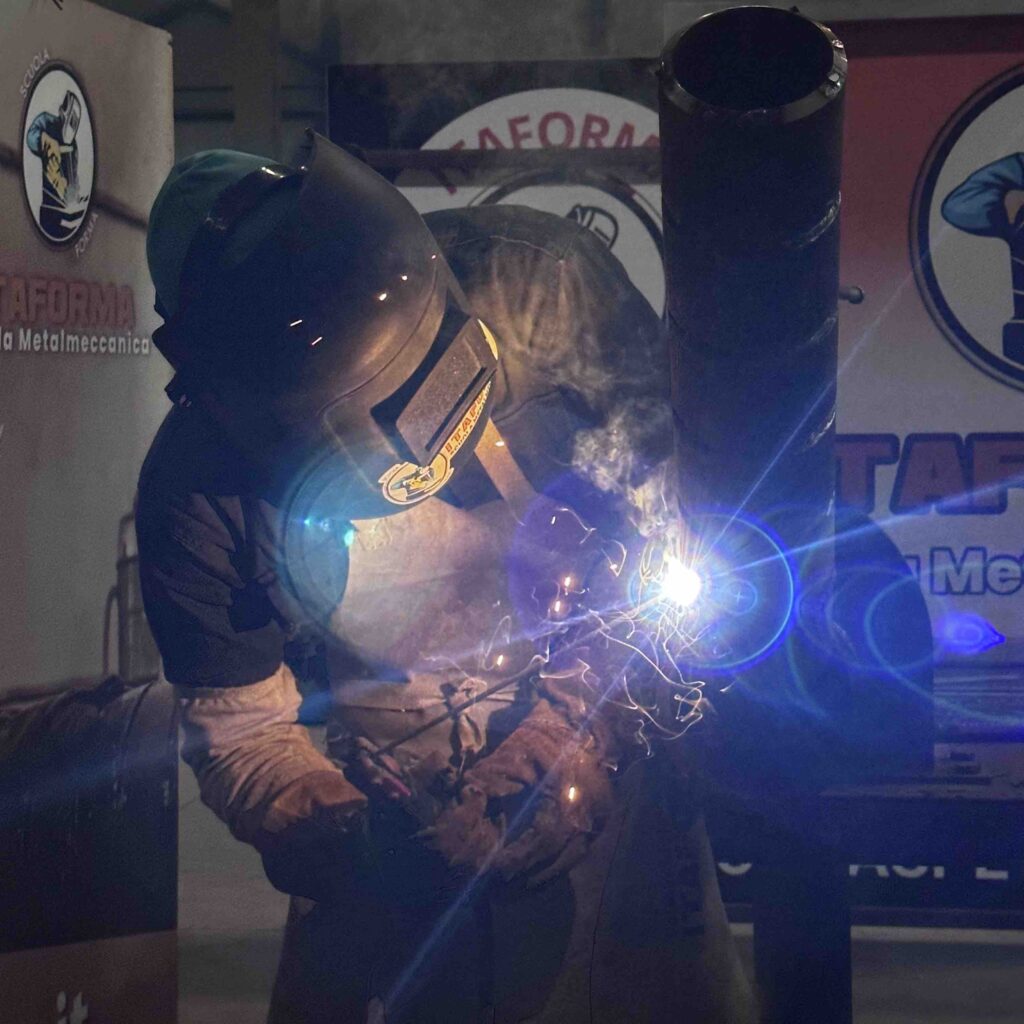
How the Process Works and Welding Conditions
To ensure the proper functioning of the electric arc, several conditions must be met:
- High voltage: required to create the electric arc.
- Sufficient current: to maintain arc stability.
- Ionizable medium: allowing current to flow between the electrodes.
Arc initiation (creating the electrical discharge between the electrode and the workpiece) must be done carefully, typically by lightly scraping the surface of the workpiece.
Improper intensity control or a rough contact between the electrodes can cause defects such as electrode sticking. Arc stability is crucial for achieving a high-quality weld and depends on several factors, including the quality of the welding machine, polarity, arc length, and the characteristics of the current (nature, frequency, intensity).
Depending on the intensity and diameter of the electrode, the welder must adjust the settings to ensure adequate penetration and avoid excessive spatter. For example, the relationship between weld bead size and electrode diameter varies depending on the type of joint (flat welding, inside corner welding, or outside corner welding).
Current Characteristics and Welding Equipment
The nature of the current plays a key role in arc welding with a covered electrode.
There are two main types of currents used in this process:
- Direct current (DC), which creates a stable arc and allows the polarity of the electrode to be selected. Depending on the application, the welder can choose direct polarity (the electrode connected to the negative pole) or reverse polarity (the electrode connected to the positive pole).
- Alternating current (AC), often used with flux-coated electrodes to improve weld stability, though it is generally less stable than direct current.
Welding equipment for covered electrode arc welding typically includes a current generator, an electrode holder, and a ground clamp. Depending on the work type and required intensity, transformer characteristics can vary, including open circuit voltage (U0), intensity adjustment range, and duty cycle.
Professional Applications and Advantages of Arc Welding
Arc welding with a covered electrode is widely used across various industries due to its versatility and ease of use. Key areas of application include:
- Shipbuilding and boiler manufacturing, where weld strength is essential.
- Civil engineering, for assembling heavy metal structures such as bridges and industrial buildings.
- Oil and gas industry, where welds must withstand extreme conditions.
- Maintenance and repair of infrastructure, including industrial equipment and machine repairs in mechanical workshops.
- Repair of old metal structures, particularly when working on rusty or damaged parts.
Thanks to its ability to be used in outdoor environments (even in windy or humid conditions) and in confined spaces, this process is particularly suited to construction work.
Its ease of use, low equipment cost, and the durability of the welds make it the preferred choice in many industrial sectors.
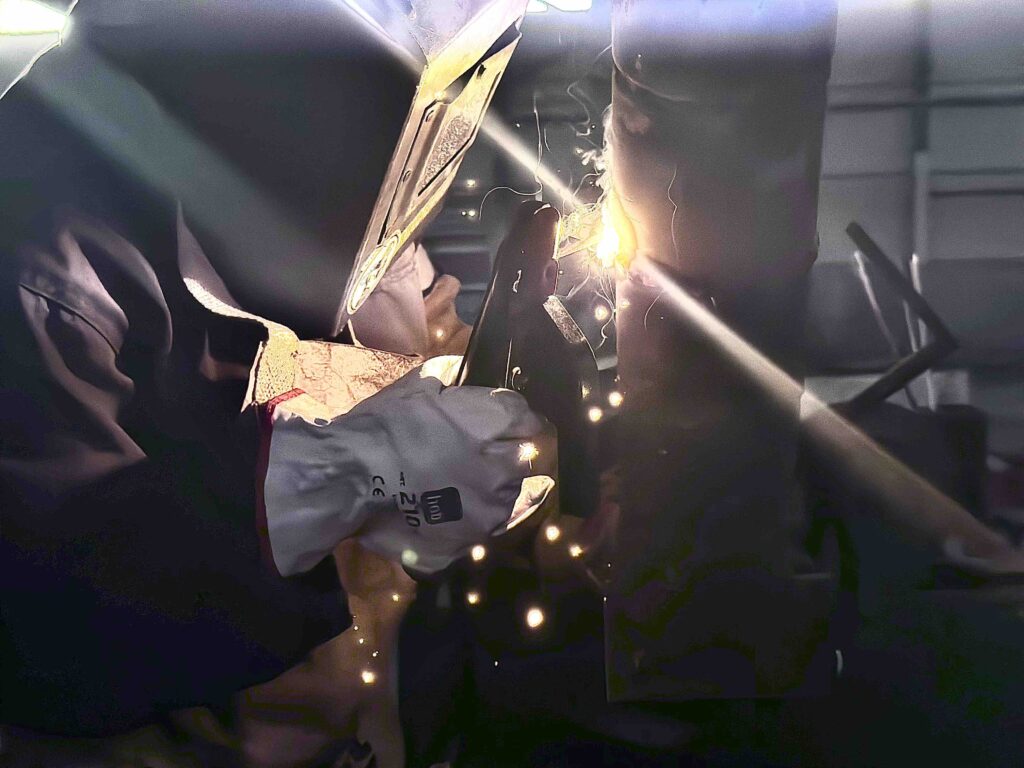
The Importance of Practical Training to Become a Skilled Arc Welder
Arc welding is a technical skill that cannot be mastered through theory alone; practical training is essential to becoming a competent welder.
While understanding the basic principles of welding, types of currents, and materials is important, it is through repeated practice that a welder gains the dexterity needed to create strong and durable welds.
Precise manipulation of the electrode, controlling the arc length, and adapting to variable working conditions (such as different welding positions, weather, or material types) require hands-on experience.
A good welder must know how to adjust welding parameters (intensity, voltage, polarity) according to the specifications of the task at hand. Moreover, the ability to diagnose and solve common issues, such as electrode sticking, excessive spatter, or an uneven weld bead, relies on solid practical experience.
Specialized training centers and apprenticeship programs offer future welders opportunities to work on real projects and receive valuable feedback from experienced trainers.
Additionally, safety standards in welding are crucial and must be incorporated into the practice from the outset. Learning to manage risks associated with extreme heat, gas emissions, and flying metal shards is essential not only to ensure the quality of the work but also to safeguard the welder and their colleagues.
In summary, while theoretical knowledge is indispensable, it is practical experience that enables the welder to develop the technical skills, precision, and judgment necessary to succeed in this demanding profession.