ITAFORMA is one of the very few welding schools in Europe certified
UNI EN ISO 9001:2015
by IIS CERT Istituto Italiano della Saldatura.
In order to obtain this important certification, ITAFORMA had to demonstrate very high quality standards in conducting its training courses.
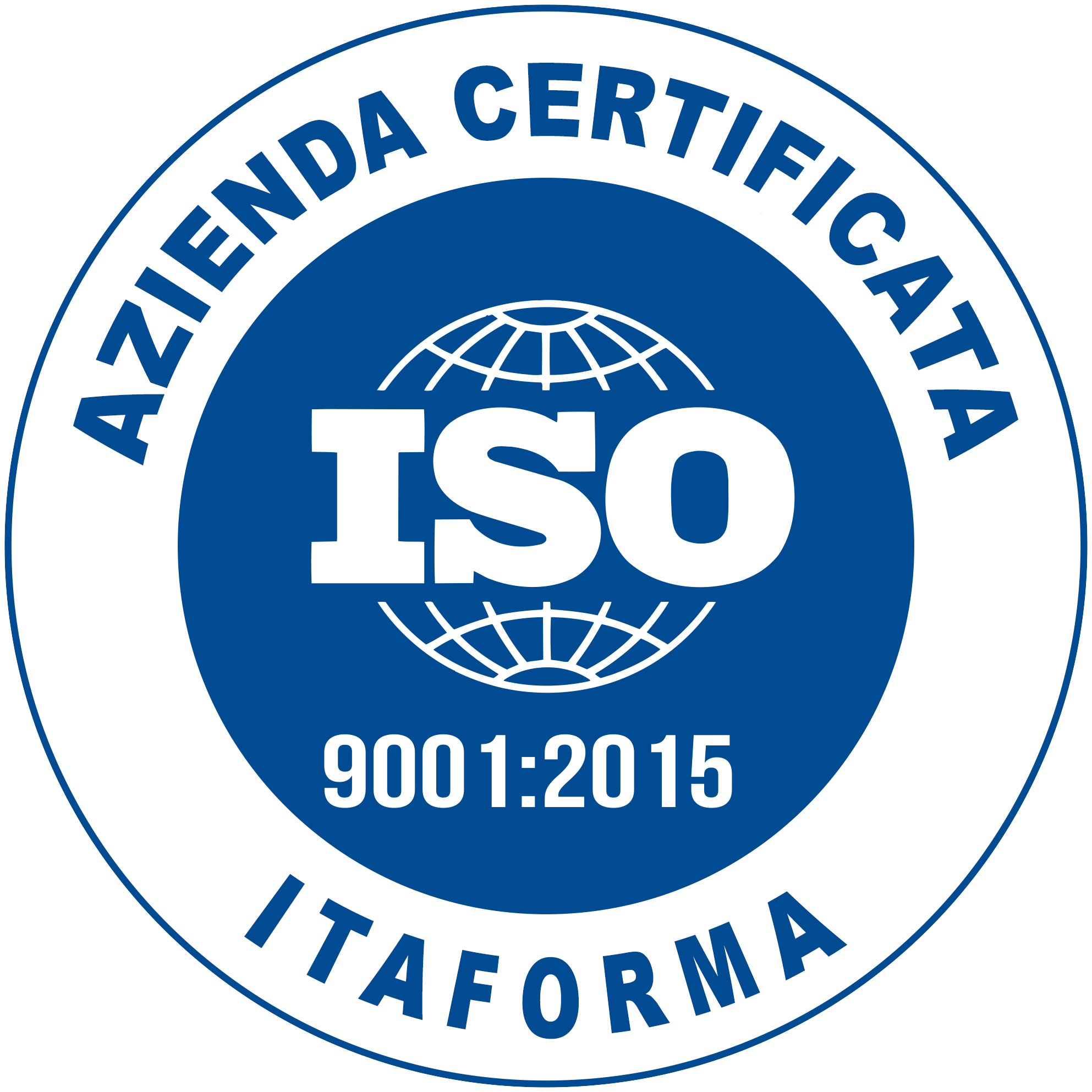
UNI EN ISO 9001:2015
A Technical Analysis of the Quality Management System.
Adoption of the UNI EN ISO 9001:2015 standard is a strategic step for organizations wishing to optimize their processes and ensure continuous quality improvement. This international standard provides an effective framework for implementing a robust and integrated Quality Management System (Q MS).
Let us take a closer look at the technical details and implications of this standard.
Structure and Fundamental Principles
The UNI EN ISO 9001:2015 standard is based on seven quality management principles, which form the foundation for its implementation:
1. Customer Focus: Organizations must understand and meet customers' needs and expectations, ensuring that their feedback is used to continuously improve products and services.
2. Leadership: Management must demonstrate leadership and commitment by creating an environment that fully involves staff in achieving organizational goals.
3. Staff Involvement: All levels of the organization must be involved and valued, recognizing that the contribution of each individual is essential to the success of the QMS.
4. Process Approach: Managing activities through interconnected and integrated processes enables more consistent and efficient results, facilitating control and continuous improvement.
5. Improvement: Continuous improvement is a central goal of the standard, pushing organizations to continuously optimize their performance.
6. Evidence-Based Decisions: Analysis and interpretation of data are critical to making informed and effective decisions, reducing uncertainty and increasing reliability.
7. Relationship Management: Maintaining strong relationships with stakeholders, including suppliers and partners, is crucial to improving the value chain and ensuring long-term sustainability.
Innovations and Flexibility
The 2015 version of the standard introduces significant innovations from previous versions, with greater emphasis on:
- Risk and Opportunity Management: The risk-based approach helps organizations identify and mitigate potential risks, as well as capitalize on opportunities to improve quality and competitiveness.
- Document Flexibility: The standard allows for greater flexibility in QMS documentation, enabling organizations to tailor documentation requirements to their specific needs.
- Integration with Other Management Systems: The high-level structure of ISO 9001:2015 facilitates integration with other management standards, such as ISO 14001 (environmental management) and ISO 45001 (occupational health and safety), promoting a consistent, systemic approach.
Implementation and Benefits
Implementing UNI EN ISO 9001:2015 requires a significant organizational commitment, but the resulting benefits are substantial:
- Improving Operational Efficiency: Process approach and continuous improvement enable optimization of resources and reduction of waste.
- Increased Customer Satisfaction: Constant focus on customer needs and improvement of product/service quality strengthen loyalty and reputation.
- Competitive Advantage: ISO 9001 certification is internationally recognized and can open up new markets, increasing customer and stakeholder confidence.
- Adaptability and Resilience: Integrated risk management helps organizations be more resilient in the face of market changes and unforeseen events.
UNI EN ISO 9001:2015 is not just a certification, but a strategic tool to promote operational excellence and support the long-term growth of organizations.
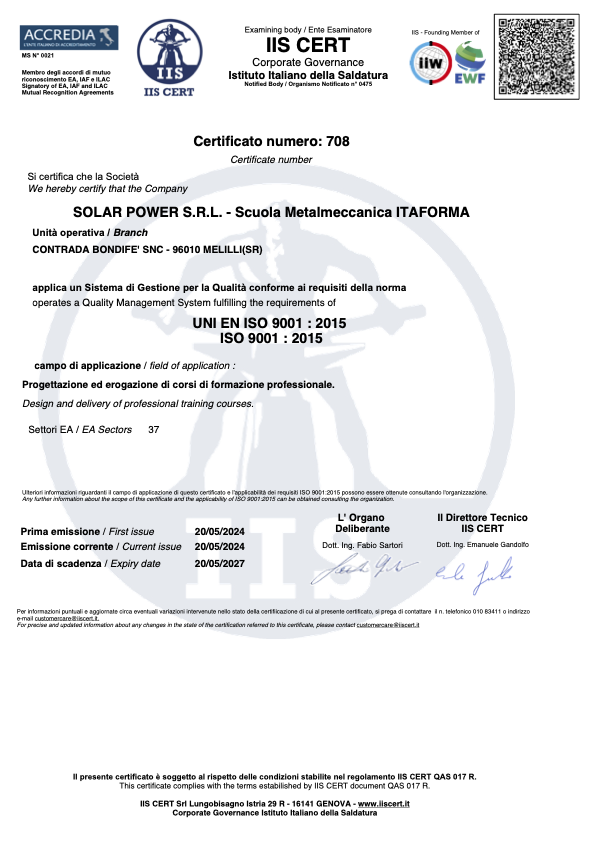