Construction of a stern platform using TIG welding
In this article we would like to briefly tell you about a our TIG Welding Course student, who had the opportunity to actively collaborate with a Tuscan company in the nautical industry.
We are talking in this case about the company Black Sail of Grosseto, which for the past 6 years has been actively engaged in the production of nautical accessories and equipment (both for boaters and for port activities) using 100% made in Italy materials, all rigorously assembled in a handcrafted manner.
In this case, the task on which our trainee-welder ventured concerns the construction of a stern platform using TIG welding; a brief description of the processing steps that led to the completion of the nautical accessory will be given below.
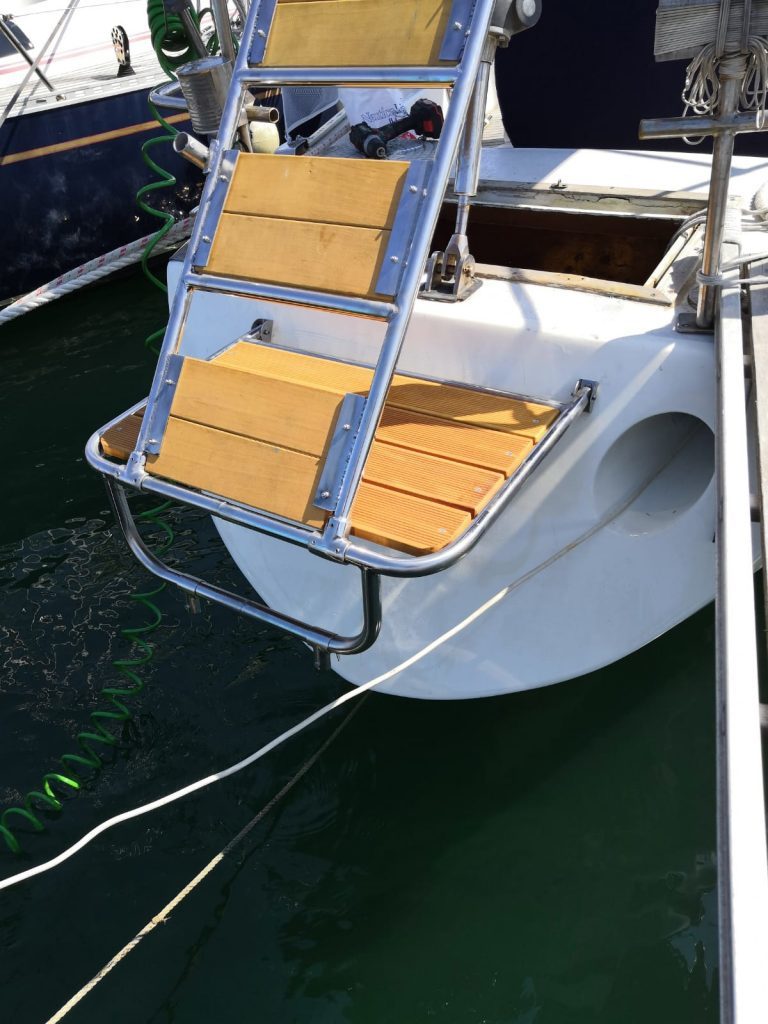
Construction of the Stern Bridge
First, however, here are some clarifications!
The stern platform turns out to be one of the most popular boating accessories; it is especially useful to have more space in the boat, in fact, many people mount the life raft right under the stern platform so as not to occupy a locker in the boat. It is especially useful for getting on and off the docks, it is also a great support for taking a shower when getting back into the boat after swimming to avoid getting wet inside.
It is also useful for supporting a walkway or attaching a climbing ladder to it and is an item, both functional and aesthetically appealing, especially when made from quality materials; usually tubular AISI 316 mirror-polished stainless steel is used to make them.
The TIG welding method has been used for this kind of work; this is an arc welding process that is carried out by means of an infusible tungsten electrode, under the protection of an inert gas. This is a particularly widely used welding methodology (and developed as early as the first half of the 20th century for war production in the aircraft industry), but it requires the use of highly skilled operators, as well as excellent quality of the materials used (remember that they will have to be cut, cleaned and trimmed).
Below are the steps for making the stern platform
DESIGN
In order to proceed with a machining operation, it is first necessary to study and be able to read a blueprint, taking into account the possible problems that may develop during welding.
PIECE PREPARATION
After studying the drawing, we move on to the fabrication of the parts to be welded, which must then be degreased by the emulsified cut of the cutting machine, trimmed from the burrs due to cutting, and drilled according to the requirements shown in the design.
ASSEMBLY AND WELDING
It is very important to always start from a suitable work surface so that the pieces to be joined are in square with each other.Once the mass is connected and the pieces are placed side by side, a "tacking" is carried out, which will help to compensate for the thermal expansion that develops with the high temperatures of welding (the effect of torsion during a weld is considerable, and it is all the more noticeable, the longer the section being welded).
Once the pieces are pointed, they are checked with the square to make sure that they are tilted correctly and that they have not undergone excessive "twisting," which in any case will be adjusted before the final welding is done.
Welding will be done in alternating sections so that any twisting will be compensated for while maintaining the desired tilts.
The resulting welds will already be firmly joined by fusion, but it is always advisable to contribute filler material to increase their strength.
PICKLING AND CLEANING
Once the welds have been cooled, pickling can be performed; this is a chemical process that removes the burnishing immediately from steel subjected to high temperatures.
Reaction with these chemicals is very aggressive and must be done with appropriate clothing and protection and in ventilated environments.
Laying and use times should always be respected even if it seems that it did not work properly as only after a final wash can the actual result be seen.
FINAL CAUTIONS
Since we work with AISI 316 stainless steel which is the steel par excellence for boating, this type of steel once heated loses its qualities and if not properly treated (pickled and polished).
Polishing involves applying additional chemical reagents that revive the characteristics of 316 steel deteriorated by high temperatures.
Once these products have also been used, it is advisable to rinse with plenty of water to remove any traces of the above agents.
If the piece we want to make requires it, it can be polished to a mirror-like surface using special brushes and pastes with graduated grits.
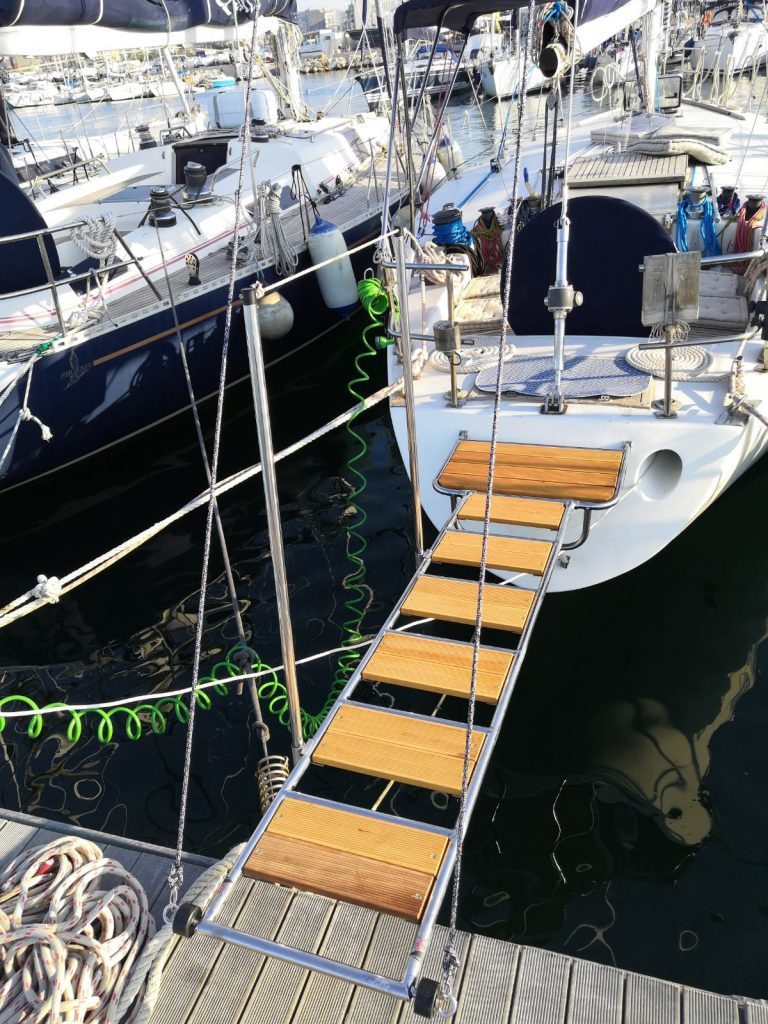